Paint bucket mould is a specialized mold used in the injection molding process to create plastic paint buckets of various shapes and sizes. The molds are designed to be durable and can withstand wear and tear. They can also be customized to meet the specific needs of customers. This makes them ideal for use in a variety of applications.
A reputable manufacturer of plastic bucket moulds can help you find the right one for your project. They can provide a range of services, including the design and production of custom-made molds. They can also perform rigorous testing to ensure that their products meet industry standards and exceed customer expectations. When choosing a plastic bucket mould manufacturer, you should consider their track record, experience, and capabilities.
Choosing the right plastic bucket mould manufacturer for your needs can be difficult, especially if you are unfamiliar with the process. There are several factors to take into consideration, including the type of mould you need and your budget. Whether you need a simple plastic bucket or a more complex mould, the supplier you choose should be able to produce a high-quality product within your desired timeframe. The best way to do this is to research the suppliers you are considering and look at their past work.
To produce a plastic bucket mould, molten plastic is injected into a hollow cavity of the mold and allowed to cool. This produces the desired shape of the finished bucket. These moulds can be made from a variety of materials, including polypropylene and polyethylene. They can be molded into different shapes and colors, and are often designed with specific features, such as handles or lids, incorporated into the mold.
When designing a new thin wall bucket Mould, it’s important to share the design philosophy with your moldmaker and allow them to make suggestions that will improve moldability. This will help you avoid costly mistakes and reduce production costs. In addition, it’s helpful to set clear guidelines about the required minimum thin wall bucket Mould life and capacity before manufacturing begins.
The cycle time of a thin wall bucket Mould is shorter than that of thicker-walled parts, which can save you money on expensive raw materials. However, reducing the cycle time can also increase stress concentration near corners, which may lead to cracking in thin walled components. It’s best to communicate with your moldmaker and discuss these issues before manufacturing begins. Also, try to schedule a weekly call or e-mail with your sales representative during the manufacturing process. This will eliminate assumptions and keep your project on track.
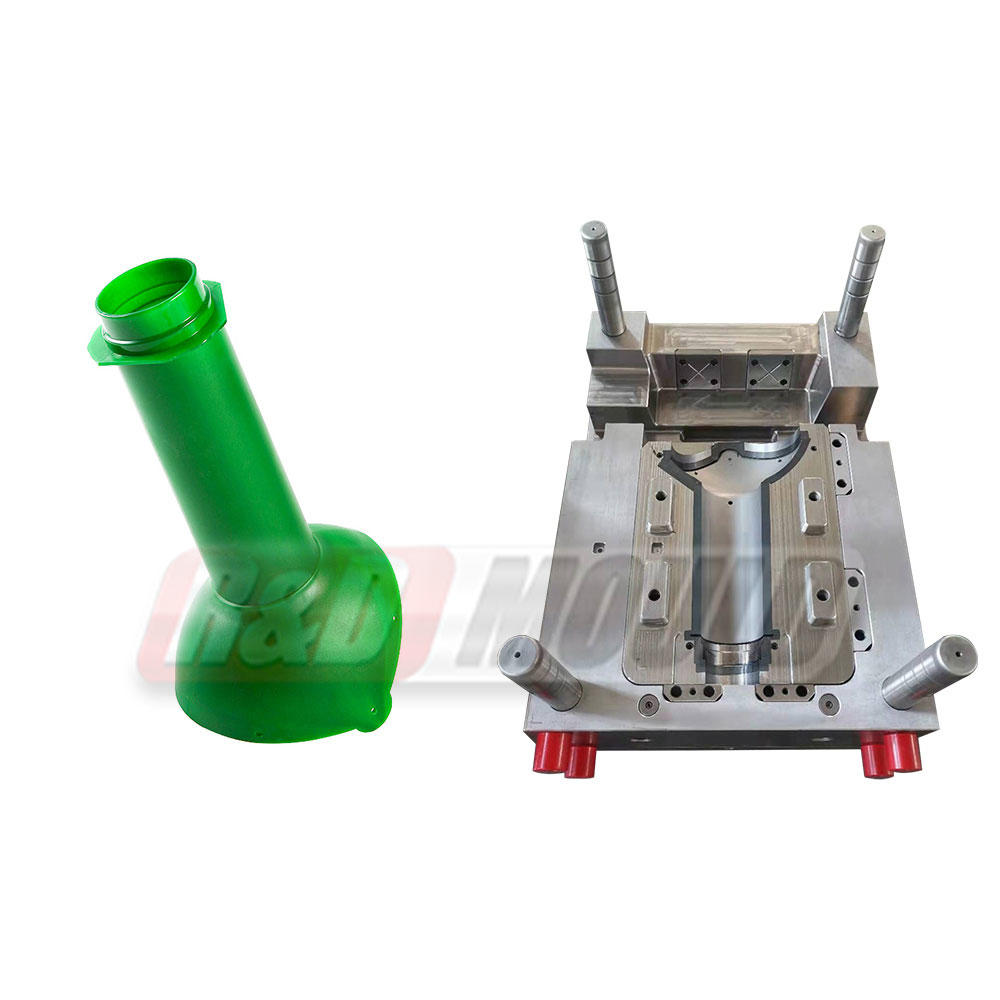