GMT can be molded into a wide variety of shapes using both injection and compression molding processes. Key suppliers on the injection side include Krauss-Maffei (Munich, Germany) and Plasticomp LLC (Winona, Minn.), while compression molders are dominated by Dieffenbacher GmbH & Co. KG (Eppingen, Germany) and Coperion Werner & Pfleiderer (Stuttgart, Germany).
In the case of a GMT composite, the raw material is delivered to the molding manufacturer in a plate-shaped semi-finished product. This is then cut into a component specific size that is then fed to the molding machine where the GMT moulded part is shaped and formed. This method of producing GMT parts has several advantages over conventional injection molded parts including cost, time and energy savings, reduced emissions and a more efficient production process.
The invention relates to a device for producing GMT plastic pressed parts comprising an upper molding tool half 6 and a lower molding tool half 7 cooperating with it, where the male and female molding tools in the closed state delimit a first cavity 8, which is complementary to the shape of the main body 2 of the GMT plastic pressed part 1, and additional cavities 9.
An important feature of the invention is that the plunge edges which define the second cavity forming the soft component in the GMT plastic pressed part have a gap which is smaller than the gaps between the plunge edges which form the edge regions of the first cavity in the GMT plastic pressed part 2. This ensures a good melt connection and prevents strong burr formation.
In the late 1990s, molding machinery OEMs developed inline compounding (ILC) systems to enable direct long-fiber thermoplastic (D-LFT) molding processes. This allows the molder to combine resin, reinforcement and additives directly in the press to form a measured shot or charge that is fed into injection or compression molding equipment for processing. This eliminates the need to store multiple formulations of precompounded LFRT or GMT pellets, and D-LFTs can be produced at a lower cost than precompounded LFRT.
In addition to the advantages already mentioned, the use of GMT in a sandwich construction with chopped glass mat and engineered fabrics allows GMT composites to be produced with exceptional stiffness, strength and impact resistance at very high strain rates. Such GMT composites are commonly employed in spare-wheel wells, liftgates for hatchback cars, rear-axle support brackets, heavily loaded underbody shields and pedestrian-protection beams. They can also be used to create new-generation seats and cargo storage compartments in automobiles, as well as in logistics applications such as trays and pallets.
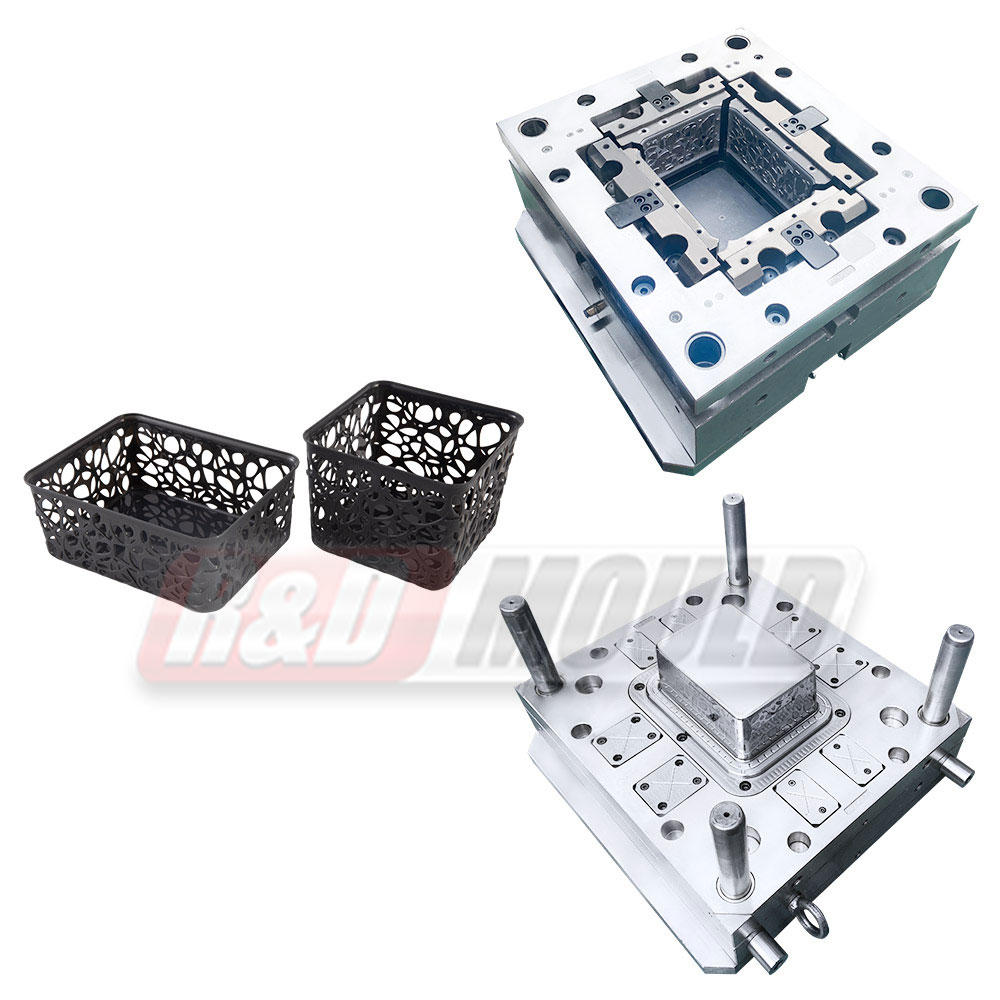