Plastic automotive molds play a pivotal role in transforming raw materials into intricate and functional automotive components. These molds are the tools that enable the precise shaping of plastic materials into parts such as bumpers, dashboards, interior panels, and even complex engine components. The use of plastic molds provides automakers with the freedom to create diverse and visually appealing designs while maintaining structural integrity and cost-effectiveness.
Design Freedom and Flexibility: Pushing the Boundaries
One of the standout advantages of plastic automotive molds is the unparalleled design flexibility they offer. Unlike traditional metal molds, plastic molds can be intricately shaped to accommodate complex geometries, curves, and textures. This design freedom empowers automotive designers to push the boundaries of creativity, resulting in vehicles that boast distinctive aesthetics and ergonomic interiors.
Lightweighting and Fuel Efficiency: A Dual Benefit
The automotive industry's ongoing quest for improved fuel efficiency has put a spotlight on lightweighting. Plastic automotive molds play a pivotal role in achieving this goal by enabling the production of lightweight plastic components that replace heavier metal counterparts. Not only does this contribute to reduced vehicle weight, but it also enhances fuel efficiency, lowers emissions, and improves overall performance.
Streamlined Production: Efficiency in Manufacturing
Plastic automotive molds contribute to streamlining the manufacturing process. The use of plastic materials, along with precise mold designs, allows for quicker production cycles compared to traditional metal components. Injection molding, a common technique used with plastic molds, enables the rapid production of identical parts with minimal post-processing. This efficiency translates to cost savings and increased production output.
Durability and Resilience: Withstanding the Road Ahead
While plastic may conjure notions of fragility, modern plastic automotive molds yield components that are durable, resilient, and capable of withstanding the rigors of the road. Advanced engineering polymers and composites used in conjunction with sophisticated molding techniques produce parts that are impact-resistant, corrosion-resistant, and designed to endure various environmental conditions.
Customization and Personalization: Tailoring the Driving Experience
Plastic automotive molds also contribute to enhancing the driving experience by enabling customization and personalization. Automakers can utilize plastic molds to create components that align with individual preferences, offering diverse color options, surface textures, and integrated functionalities. From luxurious interiors to sporty exteriors, plastic molds empower drivers to experience vehicles that resonate with their unique tastes.
Sustainable Innovations: Greening the Automotive Industry
As sustainability becomes a central focus across industries, plastic automotive molds are also evolving to support eco-friendly initiatives. Many manufacturers are adopting recycled and bio-based plastics in their molding processes, reducing the environmental impact of plastic production. Additionally, plastic molds enable automakers to design components that are optimized for recyclability and end-of-life disposal, contributing to a more sustainable automotive lifecycle.
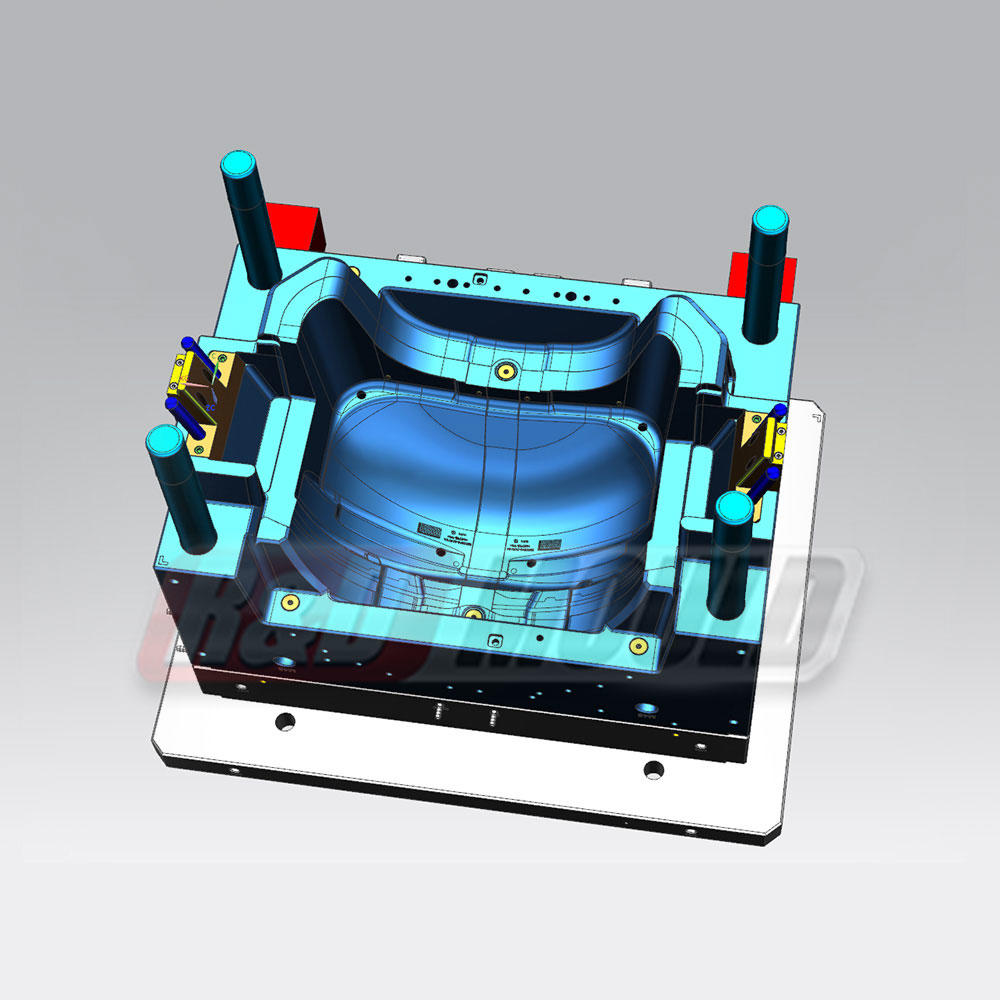