Plastic crates are containers of different sizes and shapes that can carry large and heavy items. They are used for storage and transport in supermarkets, food outlets and other businesses. The crates are made of strong and rigid plastic materials that can take many journeys before they break down or become worn out. This makes them more economical than using wooden or cardboard crates for transporting and storing goods. There are several types of plastic crates that can be made depending on the customer’s or molding company’s specifications. Some are made of a stack-nest design while others are collapsible or have a folding handle.
Crate molds can be produced by injection molding, which is a process of injecting hot melted plastic into a mould to create a solid part. Injection molding is particularly suited to the production of open crate products such as tubs, pails, cups and food containers. However, it is not suitable for the production of closed, hollow crate products such as plastic bottles. To address this issue, an inert gas is introduced into the mold before it is filled with molten plastic. This eliminates any reactions that may occur in the molded product and allows it to retain its shape.
A crate mold can be made from a variety of materials, including metals and plastics. Metals such as steel and aluminum are common choices for injection moulds, because they are durable and easy to machine. Plastics such as polyethylene and polypropylene are also popular choice for crate moulds, because they have a good impact strength and are resistant to degradation by ultraviolet radiation.
Injection crate moulds can be manufactured with either a hot or cold runner system. Hot runner systems offer many benefits over cold runner injection moulds, including faster cycle times, improved part quality and lower injection pressure. In addition, they can be used to manufacture a larger number of impressions than cold runner moulds. However, a hot-runner mould is more expensive than a cold-runner mould.
Choosing the right injection mould supplier for your plastic crate project is crucial to getting the best results. A reputable company, such as Go4mould, will have years of experience producing high-quality plastic injection moulds for the manufacturing industry. They can help you find the perfect plastic crate mould to suit your needs and budget. Then they can help you select the correct injection machine to ensure that your crate moulds are produced quickly and efficiently. You should consider the tonnage of the injection machine, shot weight, loading size and cavity of your crate mould when making this decision. You should also consider the ejection mechanism of your plastic crate mould, as this will determine how fast it can be injected and ejected from the injection machine. For example, if your crate mould has a small diameter, you will need a smaller tonnage machine than if it had a larger diameter. This is because a larger machine will have more friction and require more power to operate.
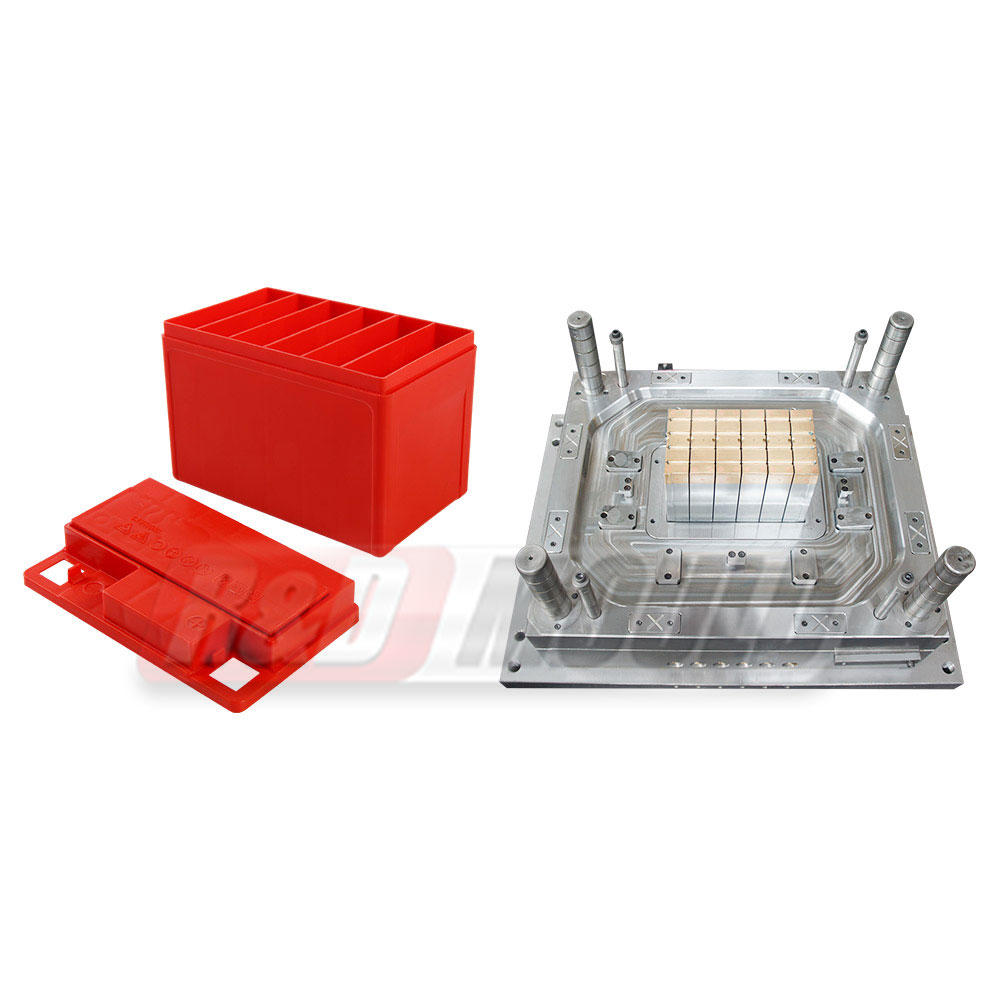