Plastic automotive molds are precision tools used to create plastic parts and components used in vehicles. These molds are responsible for shaping a wide range of plastic parts, from interior components like dashboards and door panels to exterior elements such as bumpers and fenders. Their importance in the automotive manufacturing process cannot be overstated, as many modern vehicles rely heavily on plastic components for weight reduction, fuel efficiency, and aesthetics.
Manufacturing Processes:
Design and Engineering: The journey of creating plastic automotive parts begins with meticulous design and engineering. Engineers work on CAD (Computer-Aided Design) software to create detailed blueprints of the desired component.
Mold Fabrication: Once the design is finalized, the next step is the fabrication of the mold. Skilled technicians use advanced machining tools and techniques to create molds that precisely match the CAD specifications. These molds are often made from high-strength materials such as steel or aluminum to withstand the stresses of injection molding.
Injection Molding: Injection molding is the primary process used to create plastic automotive parts. Plastic pellets are heated until they become molten, then injected into the mold cavity under high pressure. The plastic quickly cools and solidifies, taking the shape of the mold.
Quality Control: Quality control is a crucial step in the process. Molds must consistently produce parts that meet strict tolerances and quality standards. Advanced inspection techniques, including 3D scanning and dimensional analysis, ensure that each part meets the required specifications.
The Impact on the Automotive Industry:
Weight Reduction: Plastic automotive parts are significantly lighter than their metal counterparts, contributing to improved fuel efficiency and reduced emissions. Weight reduction is a critical factor in meeting stringent environmental regulations.
Design Flexibility: Plastic molds allow for intricate and innovative designs that can enhance vehicle aesthetics and functionality. Manufacturers can achieve unique shapes, textures, and finishes that are not possible with metal components.
Cost Efficiency: Plastic molding processes are generally more cost-effective than traditional metal fabrication methods. This cost efficiency can lead to lower production costs and, in turn, more affordable vehicles for consumers.
Durability and Performance: Modern plastics used in automotive components are engineered to be durable, resistant to wear and tear, and capable of withstanding harsh environmental conditions. This ensures the longevity and reliability of plastic parts.
Recyclability: Many of the plastics used in automotive components are recyclable, contributing to sustainability efforts in the industry.
Challenges and Future Trends:
While plastic automotive molds have brought numerous benefits, they also come with challenges, including ensuring recyclability, addressing environmental concerns, and maintaining high safety standards. Looking ahead, the industry is likely to see continued advancements in materials and manufacturing techniques, as well as a growing emphasis on sustainability and eco-friendly practices.
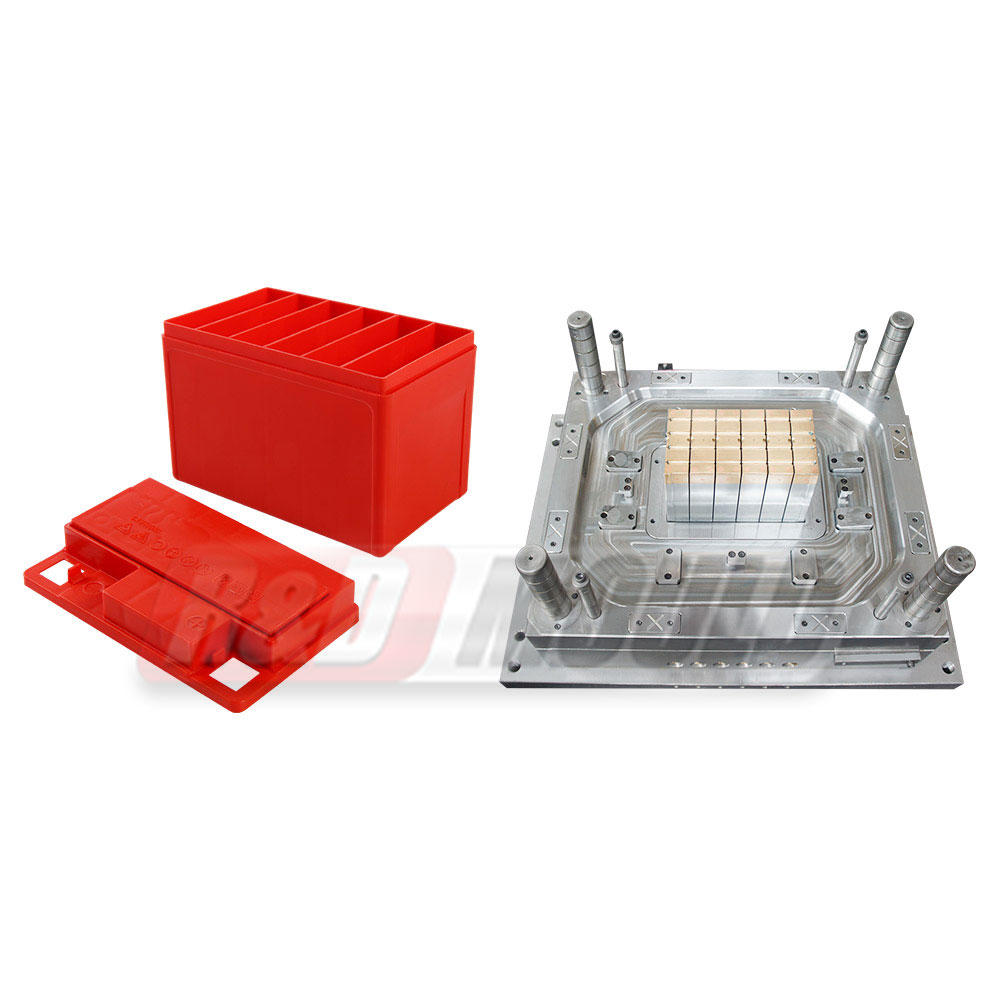