Automotive moulds are the parts of a car that are molded out of plastic. They are used in many different parts of a car, including the door mould, the windshield, and even the fenders. There are different types of moulds used in the automotive industry, including compression moulds, injection moulds, and pressing moulds.
Automotive moulds can be produced from a variety of plastic materials, including ABS and PVC. This makes them versatile, flexible, and easy to use. In addition to that, they are cheaper than 3D printing. And the more parts you need, the cheaper they get. For instance, ABS plastic is perfect for car parts because it is durable and resistant to weather. It also has excellent transparency, making it a great material for headlight covers and internal screens.
Automotive moulds are an important part of any automotive production process. It is a great help for producing parts in an efficient manner. It is important to understand the processes involved in plastic molding. First, you should know what type of moulds are available for the different types of plastic. Using an automotive mold will allow you to produce more precise and reliable parts.
In the automotive industry, plastic is the most versatile material available. It is easy to mold and can be molded into a variety of shapes. This allows automotive manufacturers to make a wide variety of parts in less time. The plastic can be mass produced, allowing them to make more products in bulk. For example, the door handles, radio dials, and light housings are often made using injection molds.
In the automotive industry, automotive plastics are used in many components, including interior and exterior structural parts. They are lighter than metal and improve fuel efficiency and vehicle performance. They are also cheaper to manufacture and impact resistant. Automotive plastics can be manufactured using the plastic injection moulding method, which allows manufacturers to produce accurate parts with intricate designs. This technique is also ideal for producing high-quality finishes. Moreover, it allows for easy spot-checking of defects. If a part is found to have a defect, it can be easily corrected by modifying the mould and manufacturing the part again.
The process of plastic injection moulding is easy and quick. It begins with a client's specifications and design. A 3D prototype of the product is then produced. Once this is complete, the product is formed inside the mould cavity with pressure protection, heat preservation, and cooling and solidification. It is important to know how to choose the right materials for the part.
Plastics used in the automotive industry are a variety of different materials. ABS is a common polymer, and is used in many different automotive parts. It is extremely durable and has a high abrasion resistance, making it a good material for interior parts. PP is also used in the automotive industry as it resists UV light, water, and chemicals.
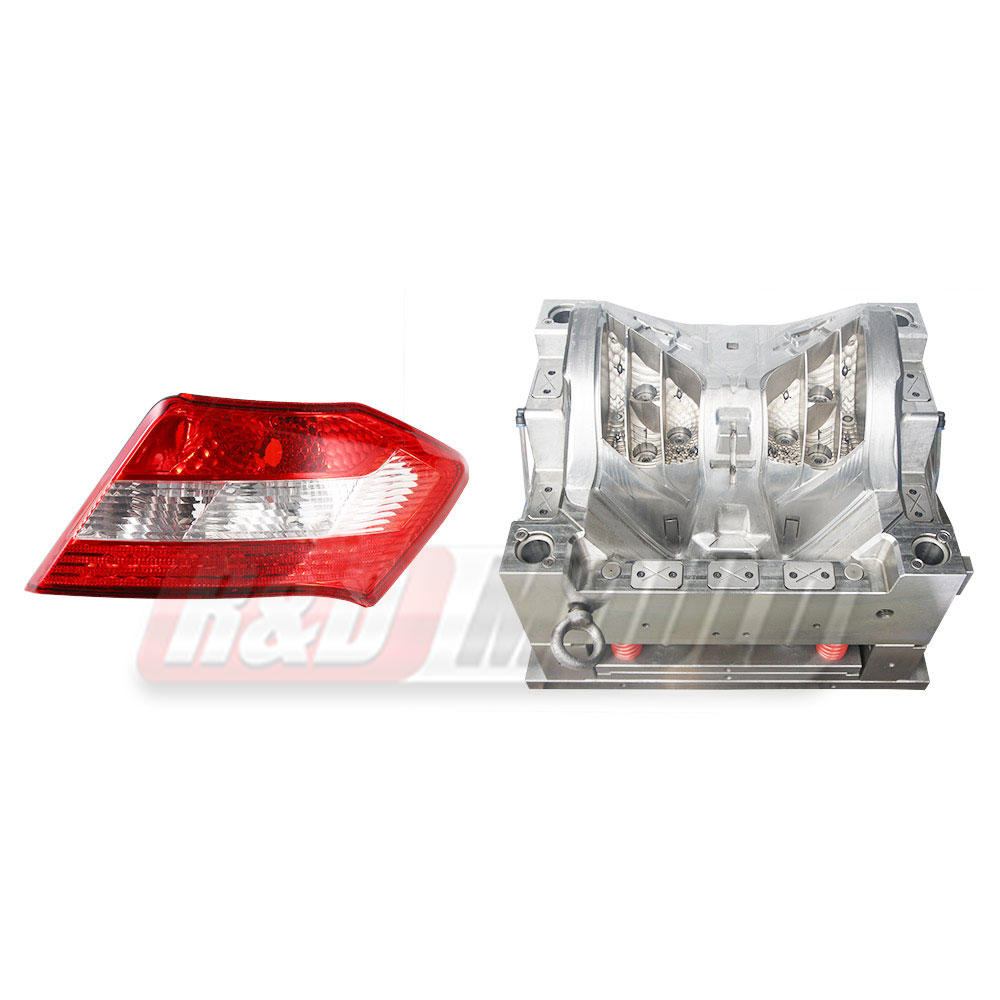
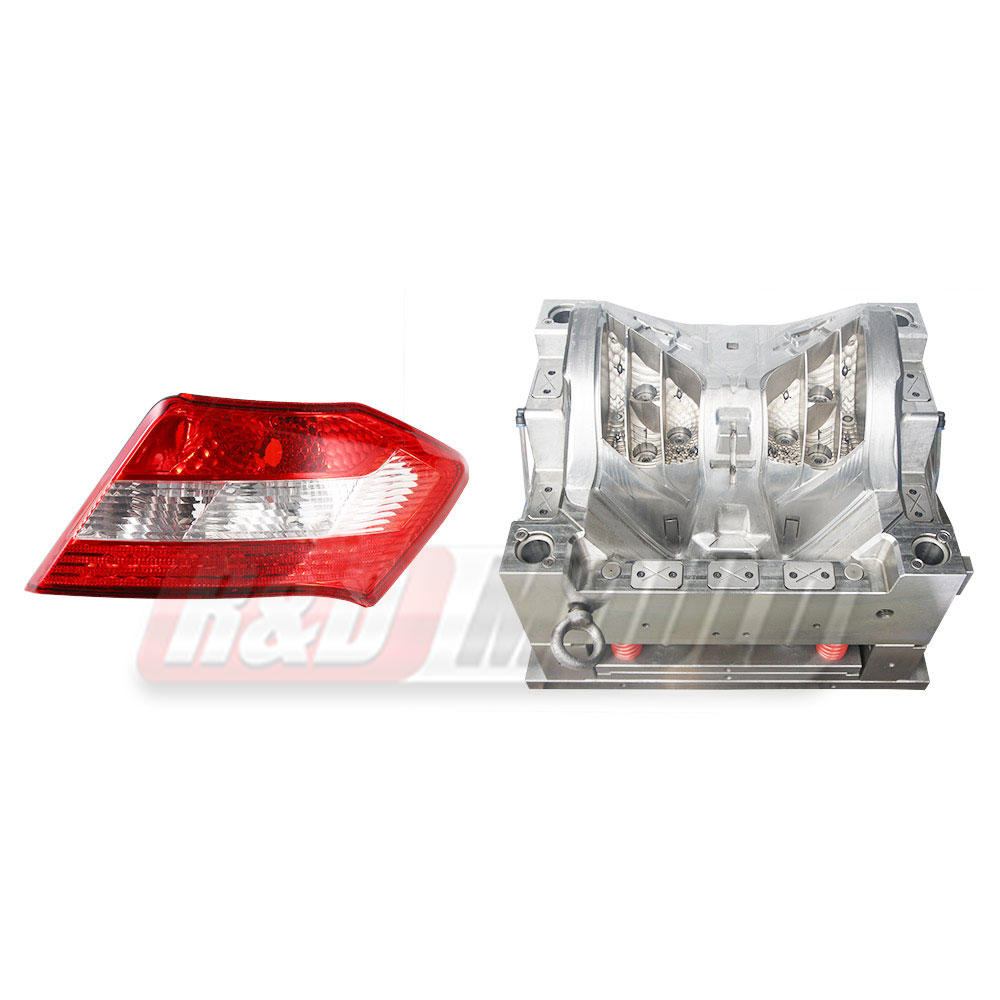