Plastic automotive molds are the backbone of modern automotive manufacturing. They are responsible for shaping a wide range of plastic parts that find their way into vehicles, from interior trim pieces and dashboard components to exterior body panels. Their significance lies in their ability to produce components that are not only lightweight but also durable, fuel-efficient, and cost-effective. The use of plastic in automotive components also contributes to reducing the overall weight of vehicles, improving fuel efficiency, and reducing emissions.
Design Considerations
Designing plastic automotive molds is a complex process that requires careful consideration of numerous factors. These factors include the type of plastic material used, the desired shape and size of the component, structural integrity, heat resistance, and aesthetic appeal. Moreover, safety is a top priority, as many components produced by these molds are critical for the vehicle's structural integrity and passenger safety.
Material Selection
The choice of material for plastic automotive molds is crucial, as it directly affects the molds' durability, precision, and performance. Common materials used for these molds include high-strength steel and aluminum. High-strength steel molds are known for their durability and longevity, making them a preferred choice for high-volume production. On the other hand, aluminum molds offer faster heat transfer and cooling, reducing production cycle times, which is crucial for just-in-time manufacturing processes.
The Mold Manufacturing Process
Design and Prototyping: The journey of a plastic automotive mold begins with the creation of a 3D CAD model. Prototypes are produced to test and fine-tune the design.
Mold Fabrication: Skilled machinists utilize advanced CNC machinery to fabricate the mold from the selected material. Precision and attention to detail are critical in this step to ensure the mold's accuracy.
Injection Molding: Once the mold is ready, it is installed in an injection molding machine. Plastic resin is heated and injected into the mold, taking its shape. This process is repeated for each component.
Cooling and Ejection: The plastic cools and solidifies within the mold. Subsequently, the mold is opened, and the newly formed automotive component is ejected. This cycle continues in a continuous production process.
Quality Control: Each automotive component undergoes rigorous quality checks to verify its dimensions, structural integrity, and aesthetic quality.
Plastic automotive molds are the unsung heroes that shape the future of the automotive industry. They are responsible for producing components that enhance vehicle performance, safety, and aesthetics while contributing to environmental sustainability through lightweight designs and fuel efficiency. The precision, design considerations, material selection, and meticulous manufacturing process of these molds are critical in ensuring the reliability and quality of automotive components.
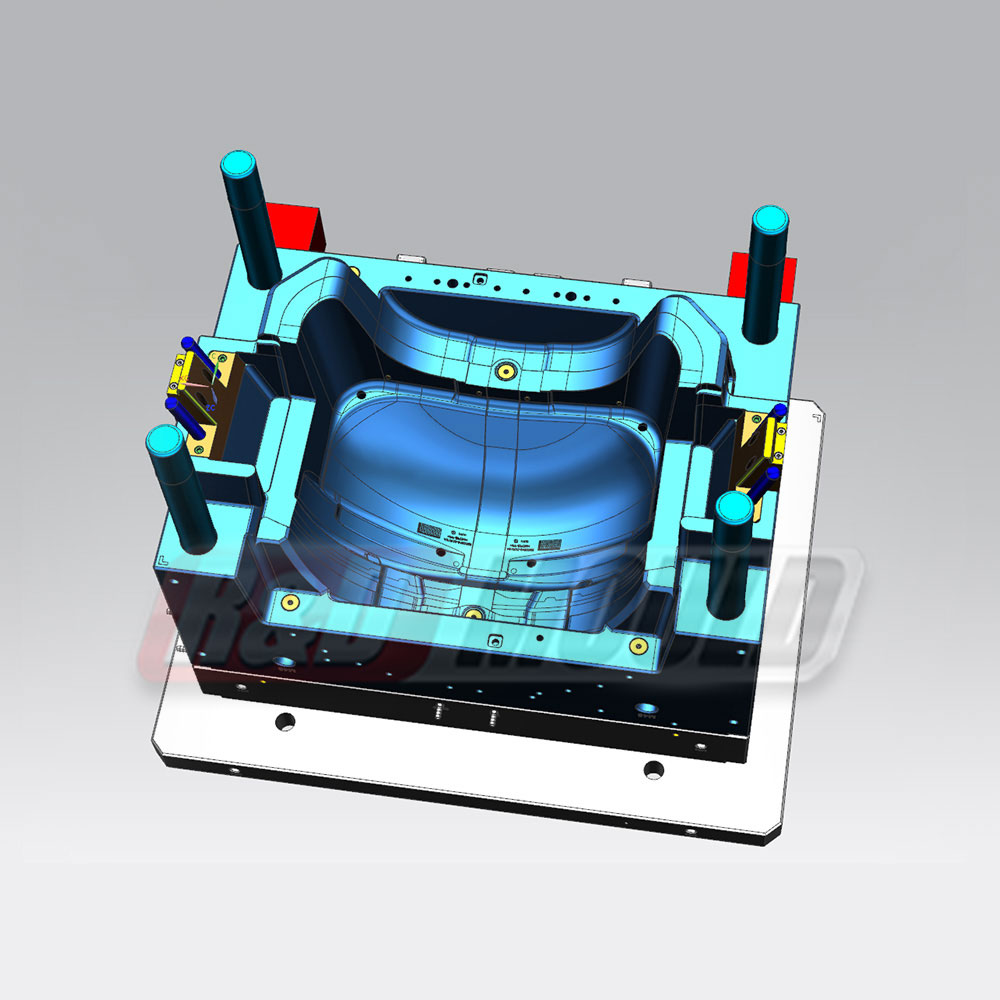