Package molds are the critical components used in the mass production of packaging materials such as plastic bottles, glass jars, metal cans, and more. They are responsible for shaping these containers with precision and consistency, meeting the stringent requirements of modern packaging needs. Whether it's the ergonomic design of a shampoo bottle, the unique shape of a gourmet sauce jar, or the durability of a beverage can, package molds ensure that these products are not just visually appealing but also functional and cost-effective.
Design Considerations
Designing package molds is a complex process that begins with meticulous consideration of several factors. The design must account for the specific packaging material, the product's shape and size, labeling requirements, and manufacturing constraints. Additionally, environmental concerns are paramount, with many companies seeking sustainable packaging solutions. Mold designers must incorporate features that minimize material waste and facilitate recycling, all while maintaining the desired aesthetics.
Material Selection
The choice of material for package molds is crucial, as it affects the mold's longevity, precision, and ability to withstand high temperatures and pressures. Common materials for package molds include tool steel, aluminum, and beryllium copper. Tool steel is renowned for its durability and resistance to wear, while aluminum molds offer quicker heat transfer and cooling, reducing production cycle times. The selection depends on factors like production volume and the type of packaging material.
The Mold Manufacturing Process
Design and Prototyping: The journey of a package mold begins with the creation of a 3D CAD model. Prototypes are then produced to fine-tune the design and ensure it meets the client's requirements.
Mold Fabrication: Skilled machinists use advanced CNC machinery to fabricate the package mold from the chosen material. Precision is paramount during this step to ensure the mold's accuracy.
Injection Molding: Once the mold is ready, it is installed in an injection molding machine. The packaging material, such as plastic resin, is heated and injected into the mold, taking its shape. This process is repeated for each container.
Cooling and Ejection: The plastic cools and solidifies within the mold, which is then opened, and the newly formed packaging container is ejected. This cycle repeats continuously during production.
Quality Control: Each container undergoes rigorous quality checks to verify its dimensions, structural integrity, and aesthetic quality.
Package mold manufacturing is an art and science that plays a vital role in shaping the products we encounter in our daily lives. From the sleek lines of a shampoo bottle to the rugged reliability of a beverage can, these molds ensure that packaging serves its intended purpose while making a statement. Design considerations, material selection, and the precise mold manufacturing process are all critical elements in crafting packaging solutions that meet consumer expectations and industry sustainability goals.
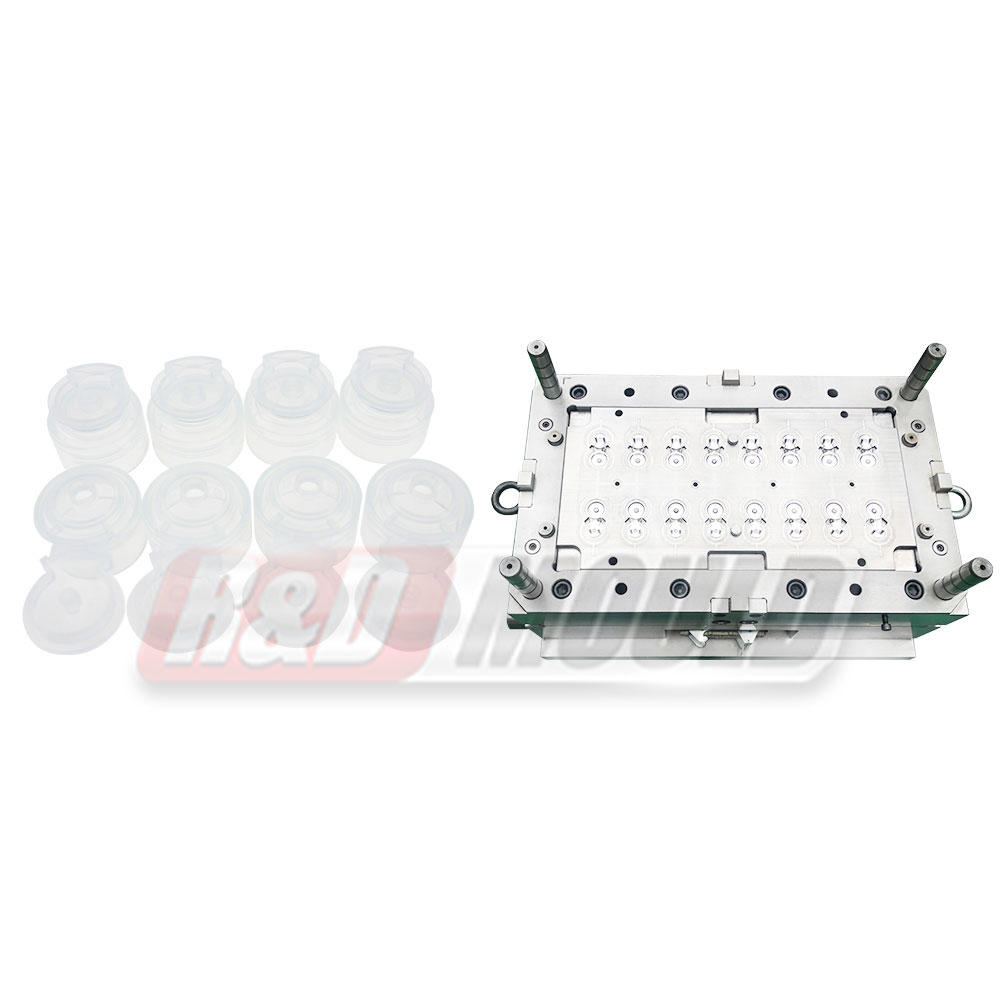