Plastic injection molds are instrumental in the production of a vast array of plastic components that are essential to countless industries. Injection molds act as precision tools, shaping molten plastic material into complex forms with impeccable accuracy and consistency. These molds play a vital role in sectors such as automotive, electronics, medical devices, consumer goods, and many more, ensuring the efficient and cost-effective production of critical parts.
2. The Creation Process of Plastic Injection Molds
Developing a plastic injection mold requires a meticulous and intricate process that combines expertise in design, engineering, and craftsmanship. Here are the key stages involved in creating an injection mold:
a. Design and Engineering: Skilled designers and engineers collaborate to create a detailed 3D model of the desired plastic component. Factors such as material selection, part functionality, and manufacturing constraints are carefully considered during the design phase.
b. Mold Making: Once the design is finalized, highly skilled mold makers transform the design into a tangible mold. This process involves precision machining, using advanced CNC (Computer Numerical Control) machinery to carve the mold cavities and cores from high-quality steel or aluminum blocks.
c. Testing and Refinement: The newly fabricated mold undergoes rigorous testing to ensure its functionality and reliability. Samples are produced using the mold to evaluate the part's quality, dimensional accuracy, and performance. Any necessary adjustments or modifications are made to fine-tune the mold for optimal results.
3. The Impact on Modern Manufacturing
Plastic injection molding, driven by injection molds, has revolutionized modern manufacturing in several ways:
a. Efficient Mass Production: Injection molding enables the production of large quantities of plastic parts with remarkable speed and efficiency. Once the mold is created, the manufacturing process becomes highly streamlined, allowing for cost-effective mass production.
b. Design Freedom and Versatility: Injection molds offer unparalleled design flexibility, allowing for the creation of intricate and complex geometries that would be challenging or impossible to achieve with other manufacturing methods. This freedom in design enables the production of innovative products and components.
c. Consistent Quality and Precision: Injection molds ensure exceptional consistency in part quality and dimensional accuracy. The molds are engineered to deliver precise and uniform results, minimizing variations and defects in the final products.
d. Material Options: Plastic injection molding supports a wide range of thermoplastic materials, including engineering-grade polymers, reinforcing additives, and biodegradable plastics. This versatility in material selection allows manufacturers to tailor the properties of the finished parts to specific requirements.
4. Advancements and Future Possibilities
Plastic injection molding continues to evolve and adapt to the changing needs of industries. Technological advancements in mold design, material science, and automation have further enhanced the capabilities of injection molding. The integration of smart technologies, such as real-time monitoring and predictive maintenance, enables improved efficiency, quality control, and reduced downtime.
Looking ahead, the future of plastic injection molding holds exciting possibilities. Advancements in materials, including sustainable and bio-based options, contribute to environmentally friendly manufacturing practices. Additionally, the integration of additive manufacturing techniques, such as 3D printing, with injection molding opens up new avenues for rapid prototyping, customized production, and increased design complexity.
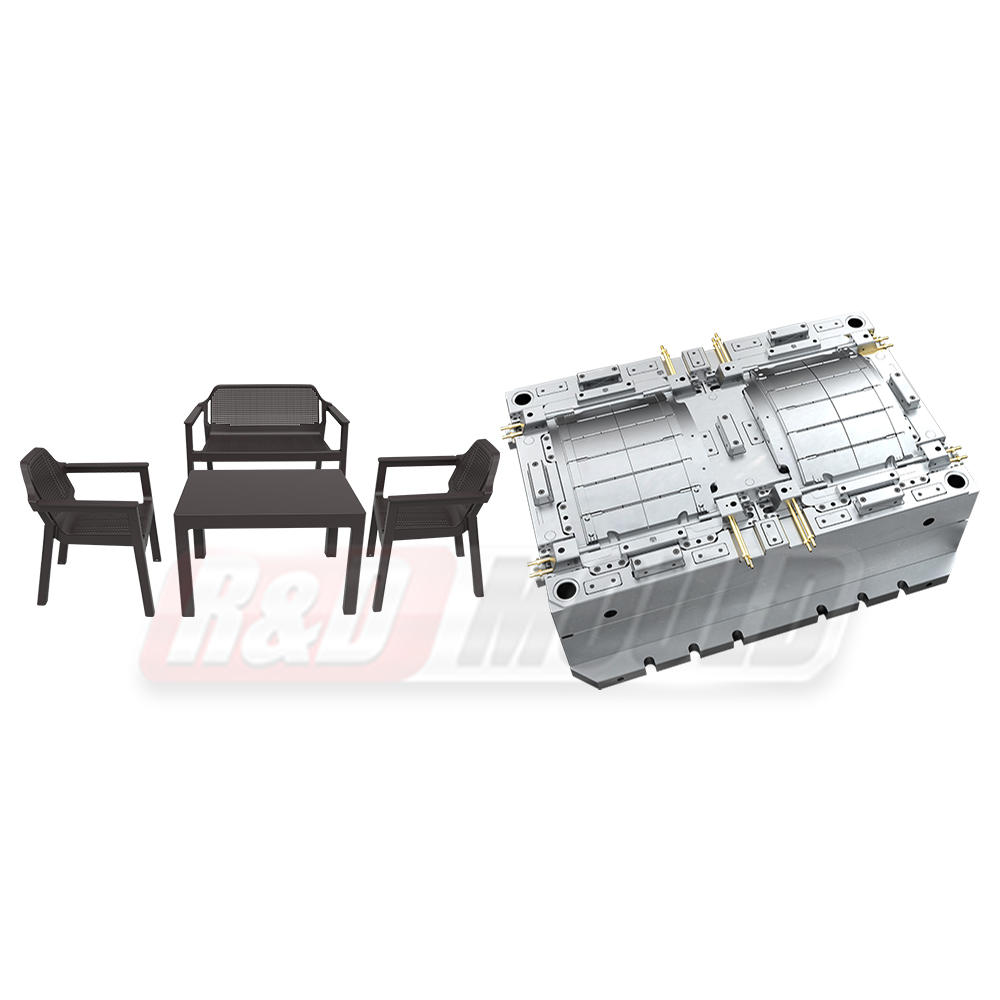