Injection molding, one of the most prevalent techniques in the manufacturing industry, is extensively used to produce different components of baby products. This process involves injecting molten material – usually plastic or rubber – into a custom-designed mold. Once cooled and solidified, the mold is opened, revealing the formed part ready for further assembly or packaging.
The ability of molds to create complex shapes and detailed designs is essential in producing safe and functional baby products. For instance, the molds used for manufacturing pacifiers need to meet strict safety standards, ensuring that the final product is free from any sharp edges or potential choking hazards.
Quality Assurance and Safety Standards
In the realm of baby products, safety is of paramount importance. Molds used in the production of these items undergo rigorous testing and adhere to stringent quality standards. These standards ensure that the materials used in molds are non-toxic, BPA-free, phthalate-free, and compliant with safety regulations imposed by relevant authorities.
Mold designs are also tailored to meet safety requirements, providing the necessary specifications to manufacture products that are durable, hygienic, and safe for infants and toddlers.
Innovation and Customization
Advancements in mold-making technologies have facilitated innovation and customization in the production of baby products. Manufacturers can create molds that offer increased flexibility and versatility, allowing for the production of products tailored to specific design requirements or changing market trends.
with the rise of eco-consciousness, there has been a growing trend towards using environmentally friendly materials in the manufacturing process. Molds have adapted to accommodate these materials, enabling the production of sustainable baby products that align with consumer preferences for eco-friendly options.
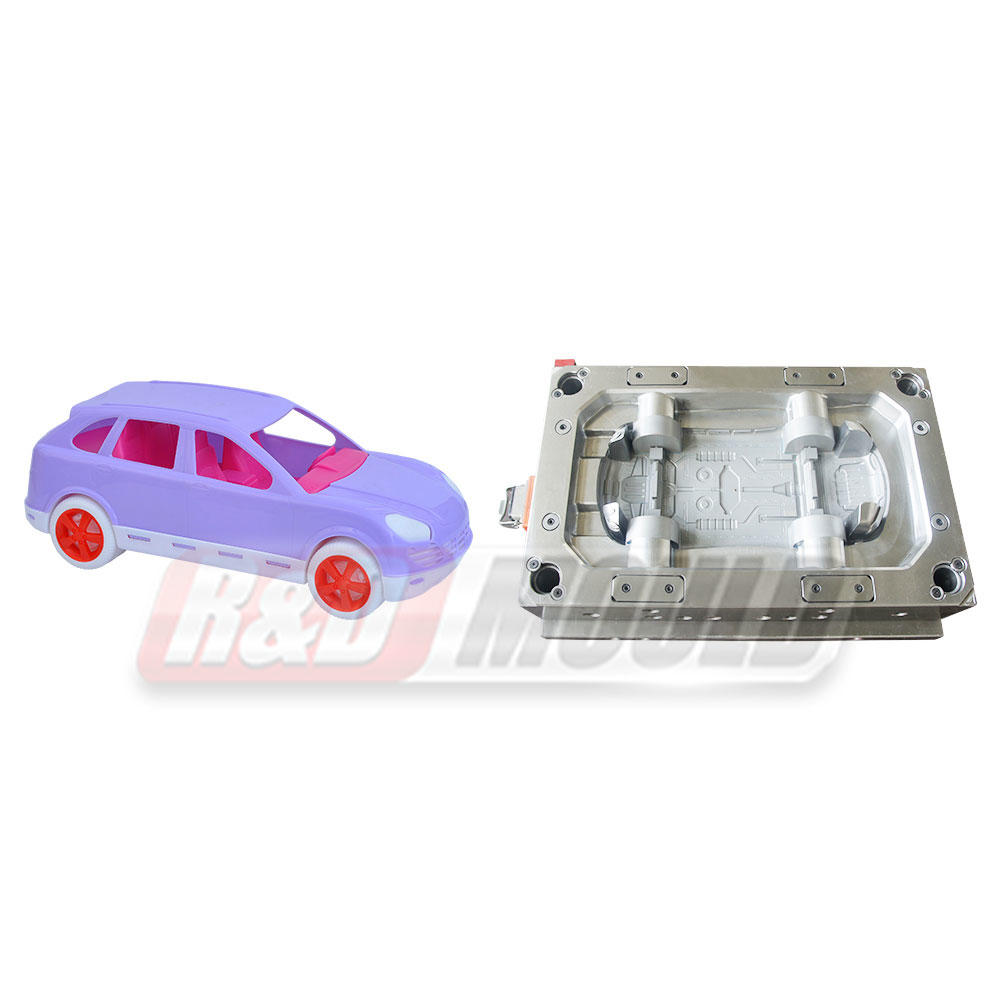